凸輪軸感應(yīng)熱處理工藝如何?
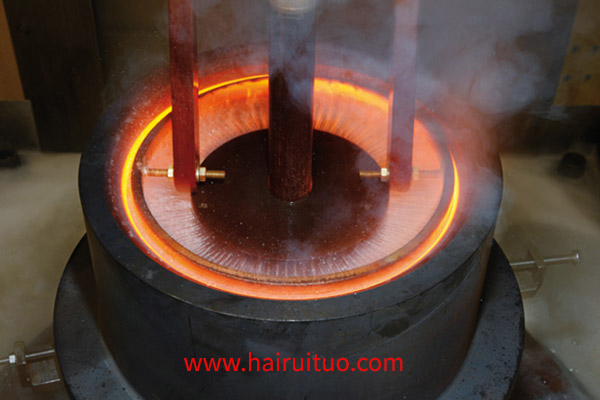
引擎凸輪軸感應(yīng)淬火的電源頻率,目前以8~lOkHz為主流,功率一般在200kW左右。凸輪軸電源頻率的選擇,主要取決于凸輪的幾何形狀。早在20世紀(jì)50年代,前蘇聯(lián)高爾基汽車廠就使用了2000Hz,200kW的發(fā)電機(jī),一次性加熱了兩個(gè)凸輪軸的曲輪。加熱5.0~5.5s時(shí),凸輪的圓弧部分高于中碳鋼的淬火溫度,而桃尖部分加熱不足,必須預(yù)冷4.5~5.Os,使桃尖和圓弧部分的溫度均勻,每個(gè)凸輪軸的功耗為3.25kW.h。使用3600Hz和200kW發(fā)電機(jī)加熱凸輪時(shí),凸輪加熱時(shí)間為3s,預(yù)冷只需2.5s,整個(gè)凸輪加熱溫度均勻,每個(gè)凸輪軸的能耗降至1.9kW.h。使用8kHz機(jī)型發(fā)電機(jī)型時(shí),加熱時(shí)間為3s,預(yù)冷卻時(shí)間明顯降低。 采用高頻、超音頻電源加熱凸輪,盡管采取桃尖部間隙增大等措施,但凸輪桃尖部溫度仍明顯高于圓弧部,該工藝已被淘汰。 (1)凸輪加熱電流頗率的選擇在沒有計(jì)算機(jī)模擬方法的情況下,曾推薦佳(Hz)的計(jì)算方式為:=3800/r2,其中r為凸輪桃尖的r值(cm)。就拿4125引擎凸輪軸來說,凸輪弧部直徑為34.9mm,進(jìn)氣門r14.14mm,排氣門r16.16mm,按上式計(jì)算:佳=3800/(0.6)2Hz=10555Hz。 該凸輪采用2500Hz加熱時(shí),桃尖溫度明顯低于圓弧部,技術(shù)上通過預(yù)冷均勻溫度提高桃尖溫度,進(jìn)行噴液淬火。 (2)凸輪感應(yīng)淬火工藝基本有兩種:分段一次加熱和整個(gè)凸輪軸一次加熱。 鋼制凸輪軸,凸輪和軸頸一般采用分段一次加熱的方式。當(dāng)凸輪和軸頸寬度接近時(shí),可共用一個(gè)傳感器。解放牌汽車凸輪軸,凸輪,軸頸,偏心,齒輪四個(gè)不同部分,共用一個(gè)傳感器,使用效果很好。這一過程的難點(diǎn)在于這個(gè)凸輪在離軸頸很近的情況下進(jìn)行淬火加熱,當(dāng)使用8~lOkHz電流時(shí),傳感器的電磁場部分會散逸到相鄰的軸頸,這樣,軸頸部分就會回火,而凸輪靠軸頸部部分的加熱溫度就會降低。如今凸輪傳感器的兩端都設(shè)計(jì)有導(dǎo)磁體,解決了這個(gè)難題。 凸輪軸工藝中遇到的第二個(gè)難點(diǎn)是兩個(gè)相鄰?fù)馆喼g的距離太近,比如相距6-8毫米。這時(shí),傳感器很難附加導(dǎo)磁體。解決方案是一起加熱兩個(gè)相鄰的凸輪。然而,由于傳感器的中間磁場較強(qiáng),傳感器的設(shè)計(jì)應(yīng)使并聯(lián)的兩個(gè)有效圈遠(yuǎn)離中間部分,并且不完全與凸輪的寬度相對應(yīng)。
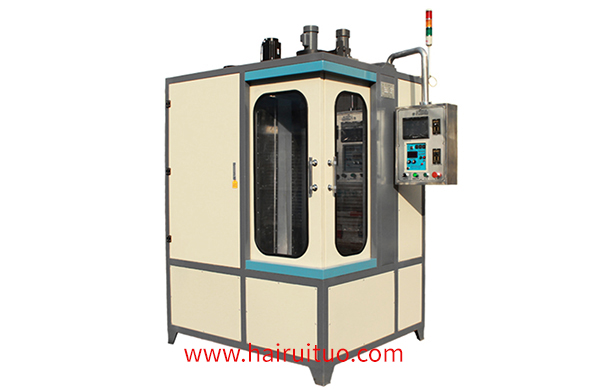
2)對于汽車合金鑄鐵凸輪軸,一般采用串聯(lián)多個(gè)傳感器,一次加熱整個(gè)凸輪軸的工藝。 (3)回火采用分段一次加熱的凸輪軸,通常采用自回火工藝。此時(shí),淬火工藝應(yīng)設(shè)置為每個(gè)加熱淬火凸輪軸的一部分,下一個(gè)加熱部分應(yīng)位于淬火部分下方。這樣可以保證淬火部分不需要第二次冷卻,有可靠的自回火溫度凸輪部分崩潰時(shí)間。凸輪由于自回火溫度不足,在下一道工序前后會發(fā)現(xiàn)凸輪部分崩潰,如圖5-18所示。有時(shí)候會產(chǎn)生很多同樣崩潰形式的廢物,有時(shí)候會因?yàn)閭鞲衅骱图訜岵糠值奈恢闷贫a(chǎn)生廢物。

(4)淬火由于鋼凸輪軸淬火表面硬度要求高,容易產(chǎn)生裂紋。一些制造商選擇凸輪軸鋼的碳含量,以縮小上下限差。例如,45鋼,選擇訓(xùn)練(C)為0.42%~0.47%,或0.43%~0.48%。 (5)凸輪軸的變形對于分段一次加熱的凸輪軸,淬火后會發(fā)生彎曲,但由于桿沒有淬硬,所以容易校正,但是對于多個(gè)凸輪一次加熱的凸輪軸,由于未淬硬的桿極短,在可能的情況下,采用校正輥,可以減少變形。